Control Surfaces
A multirotor or multicopter is controlled through the use of two or more rotors. By utilizing differential thrust management and independent speed control for each motor, the copter is able to provide lift and directional control. The added benefit of a multirotor design is encompassed in its ability to easily hold position and perform various flight maneuvers while supporting payload. Due to the innate unstable state of a multirotor, the use of on on-board computer is required to relay pilot inputs and maintain a stable flight. A multirotor, like a plane, has three degrees of rotation and hence three degrees of flight control.
Both pitch and roll are controlled through speeding up all motors on one side of the copter and slowing down the opposing motors. Hence, horizontal travel is controlled by temporarily speeding up or slowing individual motors and creating a lean in the desired direction of travel. Control in the yaw axis is controlled by speeding up motors that are directly diagonal to each other and slowing down the other set of motors. Through this motor control the copter is capable of performing a 360 degree turn while loitering at the same altitude. Finally, thrust control and changes in altitude is generated through the increase or decrease in speed of all motors simultaneously.
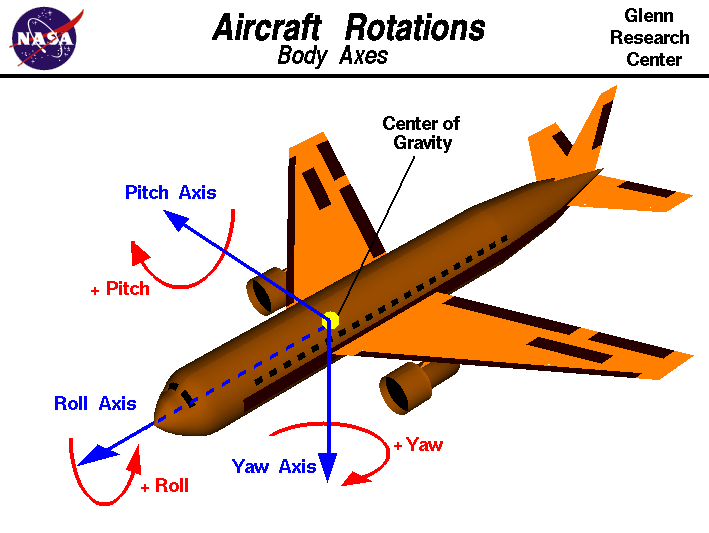
Frame Types
A multirotor is defined as any copter with two of more motors allowing for a multitude of frame configurations. Each frame configuration has inherent advantages and disadvantages, and this section will seek to examine a few various configurations.
The basic and simplest frame configuration is a quadrotor with either a + or X configuration. Both configurations are similar in the maneuverability and the control they provide. An X configuration is common when transporting photography equipment because the configuration easily lends itself to the installation of necessary equipment.
Another common configuration is a hexrotor. This configuration allows for increased payload capacity as more motors are able to provide greater thrust. The increased motors also provides an extra fail safe as the copter can be programmed to still fly in the case that one of the propellers is damaged during flight. Although these are the most commonly built configurations, the image below shows a comprehensive overview of frame builds from a trirotor to octarotor.
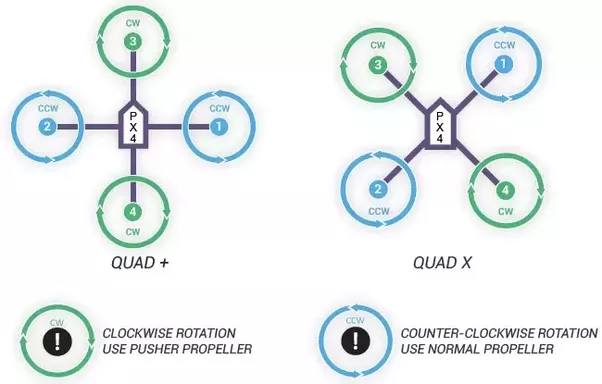
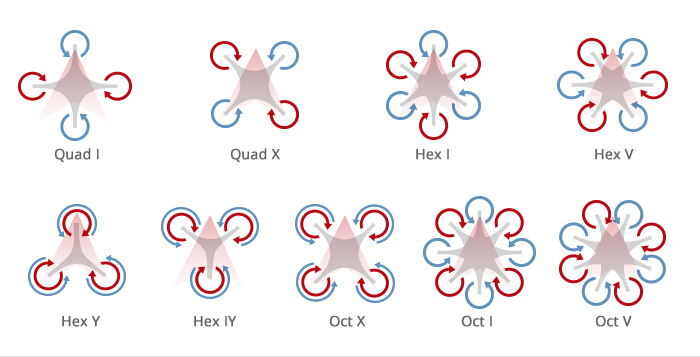